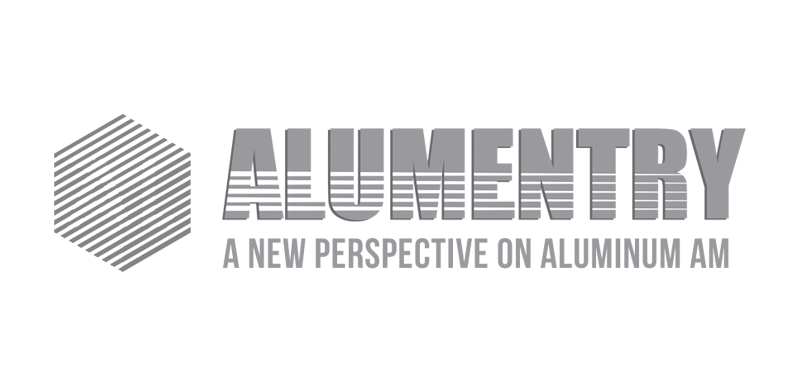
•Alumentry addresses a major pain in a huge and growing $150B industry.
•The challenge is economic manufacturing of precise aluminum parts.
•Presently, only CNC machining is capable of this precision and metal properties, but it is cost prohibitive and does not allow for simple operation, fast response time, and design freedom.
•Alternative technologies, such as casting and metal AM, cannot achieve the necessary accuracy and metal properties.
•Alumentry brings a new and promising technology, combining the accuracy and metal properties of CNC, affordability in quantity of casting and design freedom of metal AM along with the shortest delivery time of all of them.
•Alumentry will sell machines, proprietary raw material, and production capacity. It will dominate the small-medium precision aluminum parts portion of the typical CNC shop job-flow (30-60%).
Alumentry has invented, patented, proved feasibility and designs a technology that meets all 5 expectations of aluminum parts: Precision, material quality, delivery speed, free geometry and low cost.
The process uses proprietary, pre-treated aluminum foils as raw material and consists of three steps:
Precision laser marking of stacked foils.
Diffusion bonding the stack into a solid block of wrought alloy
Selective etching of the unmarked volumes in a non-toxic electrolyte.
Our go-to-market strategy emphasizes targeting job shops, CNC manufacturing, and 3D printing service providers, leveraging our technology's unmatched cost-effectiveness, precision, and labor-free automation advantages. The first stage includes partnerships through pilot programs with selected job shops, evolving into broader market penetration supported by trade shows, direct sales channels, strategic partnerships, and collaborations with aluminum suppliers.
Alumentry operates a hybrid business model focused on selling both machinery and raw materials to end users, primarily in the CNC Job-Shops markets. Our primary revenue streams include:
1. Machine sales
2. Material sales
Our revenue projections are based on the processing capacity of a single ASAM machine capable of handling 240 kg of material over a 24-hour period. Each machine is expected to operate for 250 days per year, initially functioning at 20% of its maximum capacity to reflect early-stage market entry and scaling